Heap & Partners Ltd
Heap & Partners Ltd design and manufacture industrial valves and instrumentation equipment. They are a well-established company supplying to over 60 countries worldwide. Heap & Partners offer application engineering support to their customers, enabling the provision of complete valve packages to suit individual requirements.
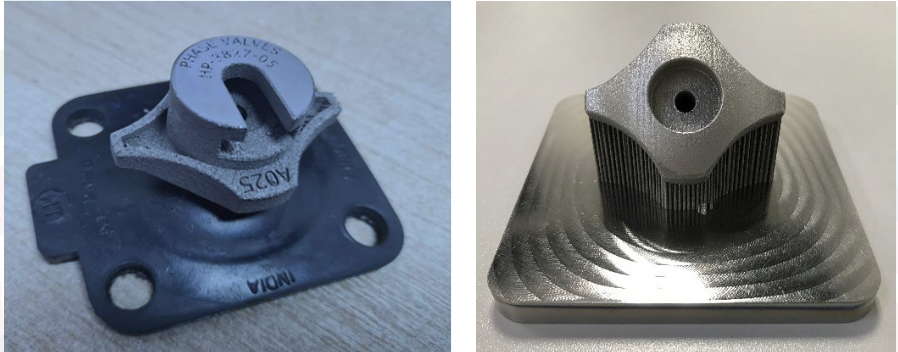
Challenge
Heap & Partners became familiar with Additive Manufacturing (AM) through a previous LCR4.0 project working with STFC. The project helped the company identify the benefits that 3D printing could add to the design and manufacture of custom parts/valves. Following on from this initial project, they decided to invest in a polymer 3D printer and continue to use this technique regularly.
Heap & Partners have now discovered applications where they envisage metal 3D printing being a valuable tool in their manufacturing process. Due to the added complexity involved in metal AM, the company are looking for advice and support in using this technology for their desired applications.
Solution
STFC’s Advanced Manufacturing Facility houses a MLab Cusing R machine, a metal powder 3D printing method. This is the most commonly used metal 3D printing technique and produces tough, durable, precise and geometrically complex parts. This technique appealed to Heap & Partners who wanted to print and test a new compressor valve design.
Heap & Partners developed the Computer Aided Design (CAD) in- house and then STFC’s Advanced Manufacturing Engineer prepared the CAD specifically for the metal 3D printing process. STFC have access to a suite of industry standard software to support the preparation process, in addition to a library of printing settings to ensure optimal printing conditions. With previous experience of producing metal 3D printed parts for the European Space Agency’s testing programme, STFC’s Advanced Manufacturing Engineer provided advice on all aspects of the metal 3D printing process; from pre- processing to post-processing methods.
As part of the 12 hours of fully funded support, STFC successfully printed the compressor valve part in a Titanium alloy, as well as sharing the methodology for the support strategy and providing a full production report.
Impact
Heap & Partners were able to use the 3D printed part to enable rapid testing of the compressor valve design. The 3D printed part was suitable for use straight away and the compressor valve functioned well with the rest of the prototype produced by machine manufacture.
Following the success of this project, Heap & Partners have identified future projects where metal AM may be able to speed up their manufacturing processes in a similar way.
For the full downloadable case study, please click here.
Once again we at Heap & Partners have been very impressed with the speed of response and support given; to help us further our knowledge in this area. We couldn’t recommend STFC’s Advanced Manufacturing more.
David Millar, Managing Director at Heap & Partners Ltd