3 steps to unlock investment and skills in robotics and automation
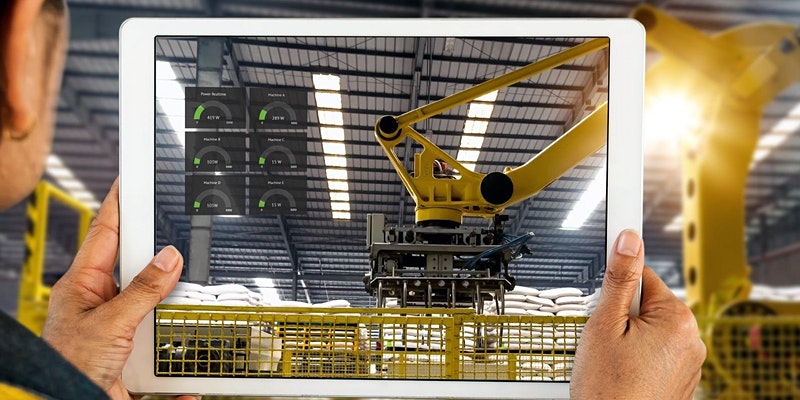
The Northern Automotive Alliance (NAA) were joined by DHL Supply Chain and the Virtual Engineering Centre (VEC) for an ‘ask us anything’ webinar which focused on the challenges that businesses face within the digital age and what support is out there to help overcome such challenges including case study examples in automation and robotics within the manufacturing and automotive industries.
Paul Jones from the NAA welcomed businesses from Klarity 4HR, Bigtank, Marks and Clerk and Viz Box Ltd to name a few as Dr Andy Levers from the VEC and Murray Goodrick from DHL Supply Chain then proceeded to take the floor for a round of slides.
Dr Andy Levers, Executive Director for the VEC
Andy started by comparing the best time for companies to start on their digital journey to the saying “the best time to plant a tree is either 20 years ago or now”, urging businesses to consider the exploration and adoption of Industry 4.0 technologies to improve delivery processes and efficiencies including within your design process which can lead to increased profitability and enhanced customer satisfaction.
Some of the technologies which were highlighted throughout the event included robotics for automation, simulations using real-time data, advanced modelling and simulation, augmented reality, AI for data analytics and even digital twin technologies. Andy highlighted how these technologies can help businesses better understand systems, processes and the integration of going on to identify bottlenecks and opportunities, offering greater insight for better-informed decision making to support your business today and futureproof against a rapidly changing environment.
Murray Goodrick, VP Business Development for DHL
Murray highlighted how smartwatch technology was a wearable solution DHL use for automotive operations. Data and information collected through scanners and smartwatches can be integrated to a wider system for better tracking and visibility, enabling better control and performance tracking of operators whilst also helping DHL to identify hazards and improve on safety concerns. Murray stated this technology can be rolled out to larger-scale operations and predicts it can improve business efficiencies of around 20%.
Murray presented their use of smart warehousing, creating a virtual window into operational data which allows for monitoring data across facilities and gives a real representation with visual aids for their control room. This platform also offers DHL the opportunity to utilise data including handling equipment, for example, identifying bottlenecks and improving productivity whilst highlighting hazardous areas for the improvement of safety within their working environments.
Poll results
During the event, we ran a multiple answer poll to ask participants ‘what are the key barriers to adoption for your organisation?’
The results of the poll were as follows:
40% – I can’t find / not sure what technology will meet my needs
20% – My employees don’t want to change the way they do things
50% – Investment in time and purchase is too costly
20% – My business isn’t ready to go through the pain of adoption
40% – I worry about switching systems. Losing control and critical data
30% – I don’t have the expertise in house to manage adoption and execution
Support going forward
“It’s you that drives your business” – Dr Andy Levers
In addition to the support the VEC and DHL can offer businesses directly, there were a number of initiatives and future groups which can offer support including the LCR4 START project, an ERDF project supporting SMEs within the Liverpool City Region to develop their digital strategy in order to prepare their businesses for digital adoption and integration.
Digital Innovation Facility, part of Liverpool’s Knowledge Quarter, bringing together world-class expertise in computer science, robotics, engineering, distributed simulation and immersive visualisation to enable collaborative R&D and support businesses linked to the exploitation of digital technologies (build finish summer 2021).
For the full recording of the video, please click here.
Case Studies
Throughout the event, several case studies were highlighted and discussed. Please find these linked below:
Genlab – Factory & Process Simulation in Manufacturing
Smart warehouse – first digital twin of a warehouse in the Asia-Pacific region for Tetra Pak. The main advantage: optimized, agile and cost-effective supply chains.
Heap and Partners – Using 3D printing and augmented reality for improved stakeholder demonstrations. This award-winning project led to further investment and upskilling of team members.
DriverNet – Award-winning project which incorporated IoT technology to enhance a competitive edge and allowed the company to further track their own CO2 emissions and better protect their IP.
Sellafield Ltd – The VEC worked with Sellafield Ltd, to co-develop a mixed reality simulator to help train and certify operatives on equipment that wasn’t yet onsite in preparation for a task in development. Another award-winning project which enabled Sellafield to save roughly £20, on costs.
Inovus – Using mixed reality in surgical training which supported product development and the penetration of new markets.
Explore more
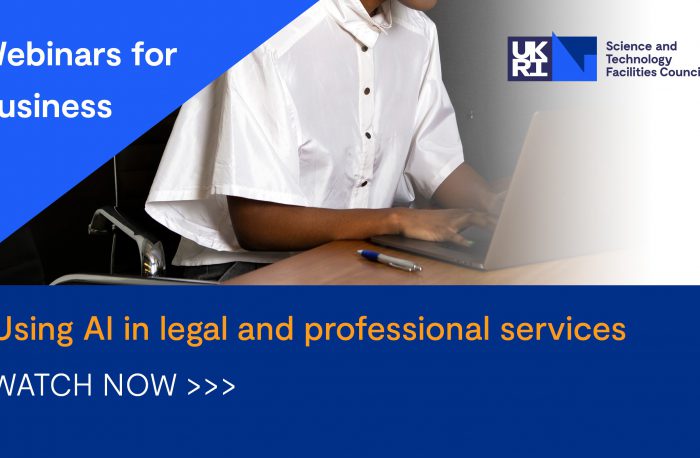
Panel Discussion | Using AI in Legal and Professional Services
On 21st January 2021, the STFC Hartree Centre talked to guest panellists from the legal…
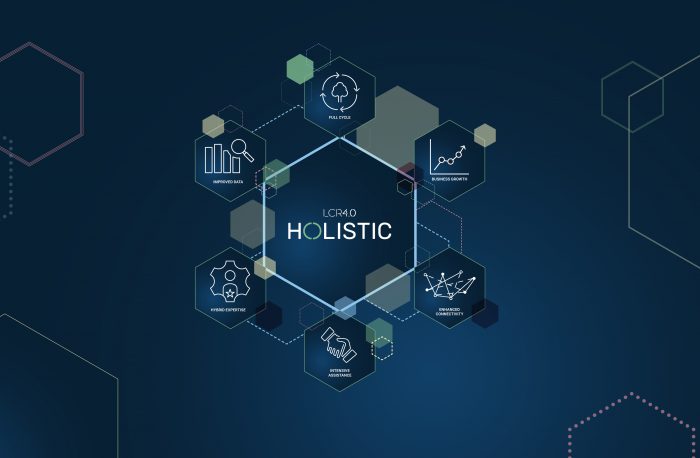
LCR4.0 Holistic supports over 50% more start-ups as a catalyst for Business Growth and Innovation
Since launching in the summer of 2020, LCR4.0 Holistic has been making great strides in…
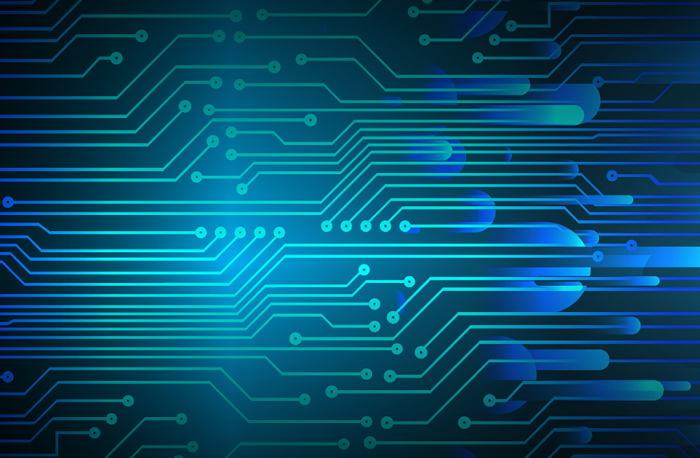
Blog: 5 Digital Trends for 2023
As we enter another year, the VEC looks ahead at our digital technology predictions for…