Heap & Partners
Heap & Partners design, manufacture and distribute a comprehensive range of industrial valves, instrumentation and associated equipment to the oil & gas, chemical, petrochemical, pharmaceutical, power & utilities, nuclear, and life science industries, worldwide.
Manufacturers of the very best flow control products available, Heap & Partners offer application engineering support to their customers, enabling the provision of complete valve packages to suit individual requirements.
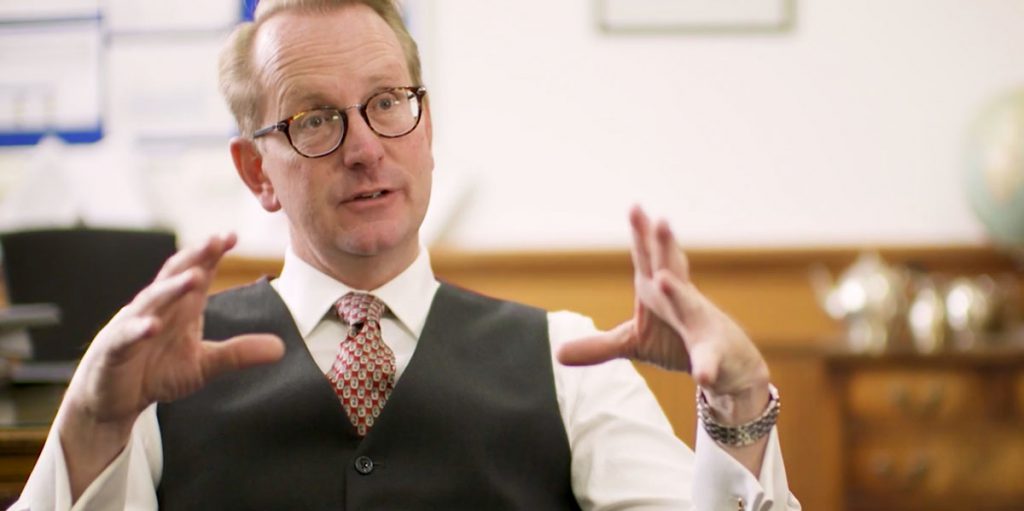
Approaching LCR 4.0
Heap & Partners wished to explore the application of additive manufacturing, focusing on improving existing 3D models and Computer-Aided Design (CAD) data skills in order to develop a 3D printed equivalent of a product. A 3D printed model could be used as a proof of concept prior to further investments and design decisions.
Heap and Partners also wanted to look into an Augmented Reality (AR) app which would allow users to explore the internal workings and components of one of the company’s valve designs.
Partner support
The Virtual Engineering Centre and Science Technology Facilities Council’s (STFC) Hartree Centre saw an opportunity to pair the two technologies as a collaborative project.
Campus Technology Hub (STFC) worked closely with Heap and Partner’s in-house design team to review and prepare an existing CAD of a large valve assembly for use in 3D printing. CTH defined moving parts and functionality of the 3D print, eventually creating a scaled down 3D printed prototype.
The Virtual Engineering Centre then produced an iOS based AR program using industry standard tools, based upon a CAD drawing supplied by Heap and Partners which act as a companion technology to the 3D printed valve.
The VEC has taken us into new areas and introduced us to new and innovative technologies, which have truly helped to transform our business. It was a wonderful collaboration.
David Millar, Managing Director of Heap and Partners
Results
STFC’s additive manufacturing team developed a valve model after revision to the size of clearances, intersecting and overlapping surfaces to allow for a smooth assembly. During a review process, Hartree’s experts offered greater insight to how the CAD model could be tailored for use in 3D printing. The result was one of the largest 3D prints produced by Campus Technology Hub (STFC).
The Virtual Engineering Centre successfully developed an AR app which operates in conjunction with the 3D printed valve. Using a tablet base application, Heap and Partners can employ this for marketing and client communication in addition to maintenance and training.
The app uses a QR code or object recognition as a trigger, whilst presenting an X-ray style AR representation of the internal workings of the valve. By highlighting a component, the user is presented with a summary of the features and technical data associated with the highlighted component, helping to expand user knowledge and awareness.
Working into the future
The Virtual Engineering Centre developed the AR application using commercially available and industry standard software packages. Heap and Partners have been supplied copies of the software model to allow for further development of the demonstrator into a commercial product.
This project demonstrates how an existing asset and skill set can be complimented quickly and easily by the adoption of Industry 4.0 technologies.
Within a few days of the project completion, Heap and Partners showcased the AR application at a trade event in Aberdeen and have also invested in a 3D printer which is to be used to undertake both development work and fulfil orders including rapid prototyping.