Goddess International Limited
Goddess International Limited is a well-known and trusted name in the design and manufacture of beauty therapy equipment. Over the last 20 years they have supplied skincare products, equipment, training and services to salons, spas and colleges throughout the UK and overseas. Their reputation has been built on the keen detail and high level of design, quality, reliability and affordability of their products.
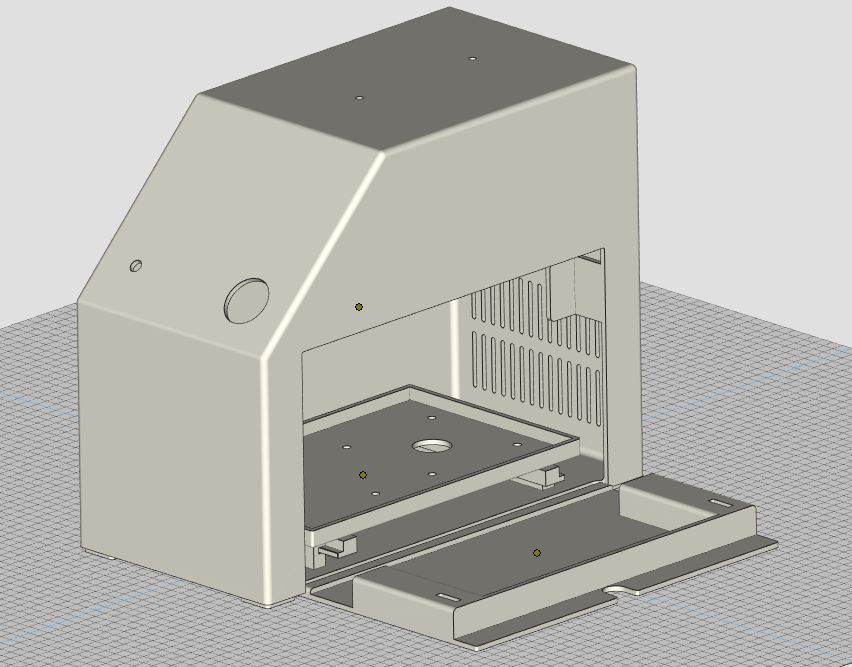
Challenge
Goddess International were searching for new sustainable methods of producing their existing equipment. They also needed to find a way to produce this in variable quantities, which is not possible with traditional manufacturing processes.
They approached the Science and Technology Facilities Council (STFC) to explore the use of 3D printing as a new manufacturing method. However, as the technology is new to them, they did not have a computer aided design (CAD), which is required to create components using 3D printing.
Solution
STFC engineers worked with Goddess International to understand the key requirements for parts for their Minipeel Compact Micro Dermabrasion System. The engineers were able to create a 3D CAD model through reverse engineering.
They used 2D technical drawings recreated by Goddess International. The CAD design ready to be used for 3D printing was finalised by taking measurements of the Minipeel Compact Micro Dermabrasion System parts.
Impact
Goddess International now have a 3D CAD model of their existing product that they can use to make prototypes using 3D printing. The dimensional accuracy, strength, robustness, and fitment of 3D components with other components in the product assembly will enable them to assess the suitability of 3D printing as a production solution.
In addition, the CAD model assists in sourcing a new long-term supplier and manufacturer as it is based on recommendations from STFC’s technical expertise.
Click here for the downloadable case study
We are so impressed with the help and assistance we’ve received from STFC for our project. Their knowledge and expertise have been truly valuable, and we are looking forward to continuing to work with them to see the outcomes of the 3D printing process.
Roz McCall, Managing Director