Dr Andy Levers explores the Skills Gap
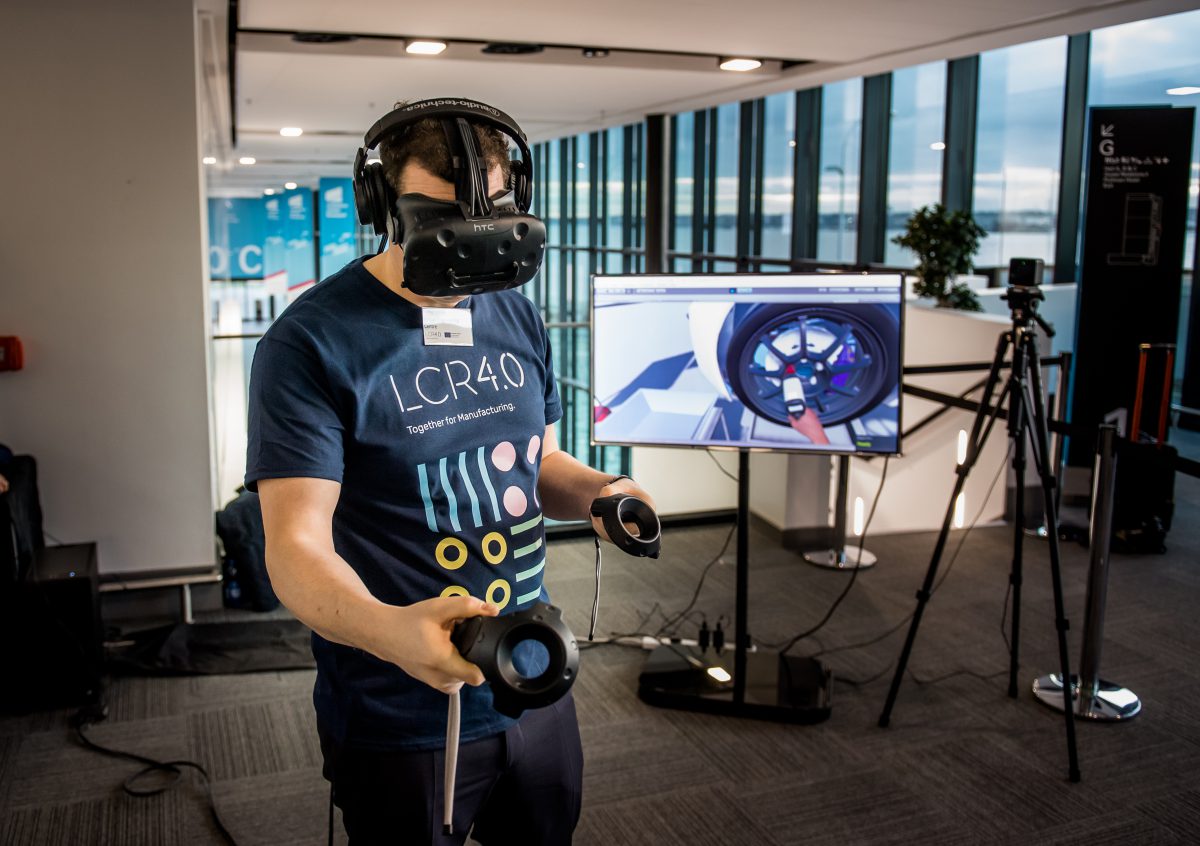
Continuously discussed amongst manufacturers within the UK and across the globe, the skills gap is a growing concern for many as the type of skills needed for smart factories are tough to source yet in high demand.
The manufacturing sector is increasingly adopting industry 4.0 technologies as more and more of the factory equipment used in everyday processes is becoming digital, through the Internet of Things and a high demand for big data for example.
Subcon in association with The Engineer recently completed a poll which targeted over 600 industry professionals. The results showed that 67% of UK manufacturers are worried about the future availability of skilled staff for their business, whilst 72% don’t believe the government is doing enough to promote skills training.
A high percentage of those asked believe that there are not enough young people within the UK’s manufacturing workforce despite careers such as engineering offering great opportunities for people choosing this career path.
The Hartree Centre based in Sci-Tech Daresbury recently held a roundtable event with a range of small and large tech businesses, all with regional interests. In summary, the results of the roundtable revealed that skills in emerging technologies such as machine and deep learning and block chain, are in high demand across all industry sectors. Soft skills are also important through human interface, project management and the ability for engaging with customers. Other skills in demand include domain skills in science and engineering including IT and programming.
The Virtual Engineering Centre (VEC) is part of the LCR 4.0 project, a part ERDF funded three year programme which focuses on supporting and helping manufacturers and SMEs based in the Liverpool City Region, to adopt industry 4.0 technologies including simulation, virtual prototyping, IP support, augmented operators, software development and more.
The VEC is planning to run several workshops where manufacturers within the Liverpool City Region can present their business and product ideas to the technical team who can advise how these ideas can become a reality.
By the business being so involved within the development process, the knowledge and new skills can be shared within their own teams and introduced throughout the business.
Another way to overcome the skills gap in the long term would be to increase apprenticeship opportunities within your business. This can allow a young budding manufacturer to learn the tricks of the trade while the business could benefit from a fresh perspective and new suggestions on how to approach certain situations.
According to the government’s skills funding agency, since February 2017 there have been 4,300 starts on new standards in occupations such as Software Developer and Aerospace Engineer. Nearly all apprentices feel they acquire or improve their skills as a direct result of their apprenticeship and after finishing, 77% of apprentices stay with the same employer. This would allow employers to not only reduce the skills gap but are then likely to achieve a new employee who is already skilled to a higher level and understand in particular the processes of that company in particular, needing little to no training or recruitment fees.
Explore more
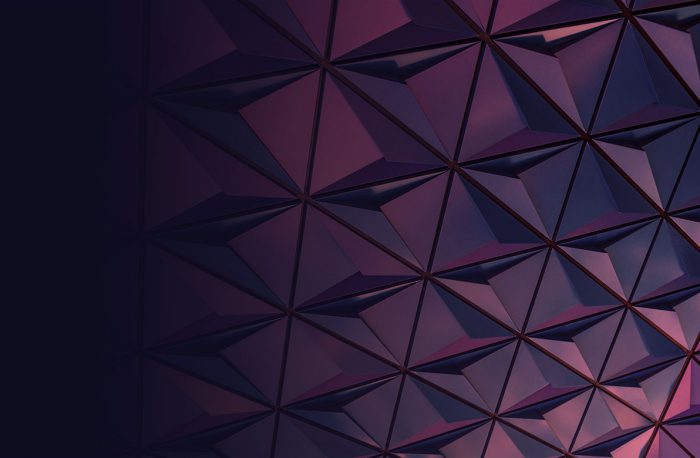
Liverpool City Region LEP offers useful insights into LCR 4.0
Earlier this month, the Liverpool City Region Local Enterprise Partnership (LCR LEP) offered a number of…
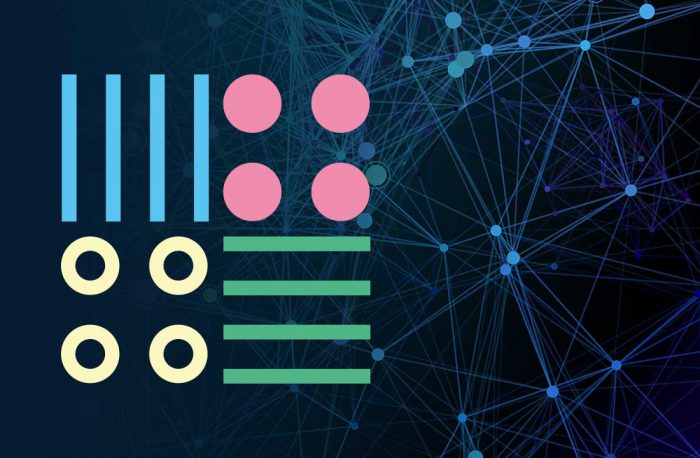
LCR 4.0 listed in Financial Times Top 100
The Financial Times has listed LCR 4.0 as one of its ‘Top 100 European digital…
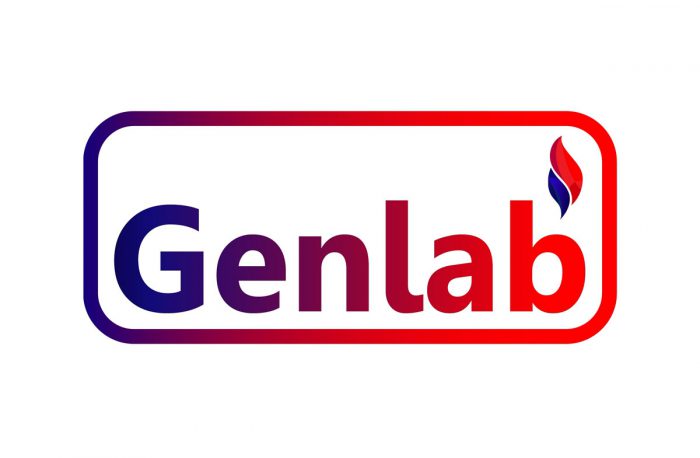
Widnes manufacturer pioneers first-of-its-kind touch-screen controller for industrial appliances
Widnes-based manufacturer Genlab has designed an innovative touch-screen controller that enables users to view and…