ESL Electromech Ltd
Based in Runcorn, ESL Electromech is a family run business that offers a range of services in the mechanical and engineering sectors, offering design, manufacture, repair and upgrade capabilities.
ESL is dedicated to providing quality service and meeting the highest standards in machining, fabrication, transformers and coils, and electrical systems. The business manufactures on-demand parts either for specific applications or for replacement of failing parts. They possess a machine workshop & fabrication workshop to do all types of mechanical repairs, specialising in a quick turnaround to enable their customers to get back into production with minimal downtime.
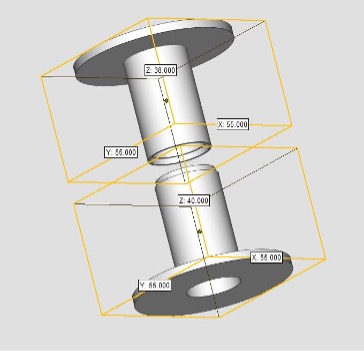
Challenge
3D-printing is a new technology to ESL; they needed support to understand the process for manufacturing parts using 3D-printing. They were aiming to explore 3D-printing technology as a means of producing components to support their business model for repairing or replacing parts within 1-2 days and answer the following:
– Suitability of 3D-printing as a production process.
– Dimensional accuracy of the 3D-printed components.
– Strength and robustness of 3D-printed components and suitability for end use.
– Fitment of 3D-printed components with other components in the product assembly.
Solution
Science and Technology Facilities Council engineers created a computer aided design (CAD) of a bobbin component. As STFC’s additive manufacturing facility has a range of 7 different types of additive manufacturing technologies, the engineers manufactured prototype parts from the CAD to assess suitability of material and design. STFC liaised with ESL to identify the most appropriate technology for their application and created prototype parts using Fused Deposition Modelling (FDM) industrial 3D-printers to produce parts in ASA (UV stable ABS) and Nylon Carbon Fibre materials.
Impact
ESL were able to test the prototype parts and understand the benefits of additive manufacturing technology. They have concluded that 3D-printing would be a viable technology for their business and are progressing with more prototype parts to further develop their knowledge with a view to investing in the technology.
To access the downloadable case study, please click here.
The support we received from STFC has been extremely beneficial to us. The LCR4 Start project has allowed us to explore the use of 3D printing as a solution to some of our manufacturing challenges. We manufacture on demand parts in a short timeframe, and we now have a broader understanding of how 3D printing can help us do this. This is a new technology for us and, with the support of STFC, we will be exploring this technology further via the C&W4.0 programme.
Edwin Santley, Owner of ESL Electromech Ltd
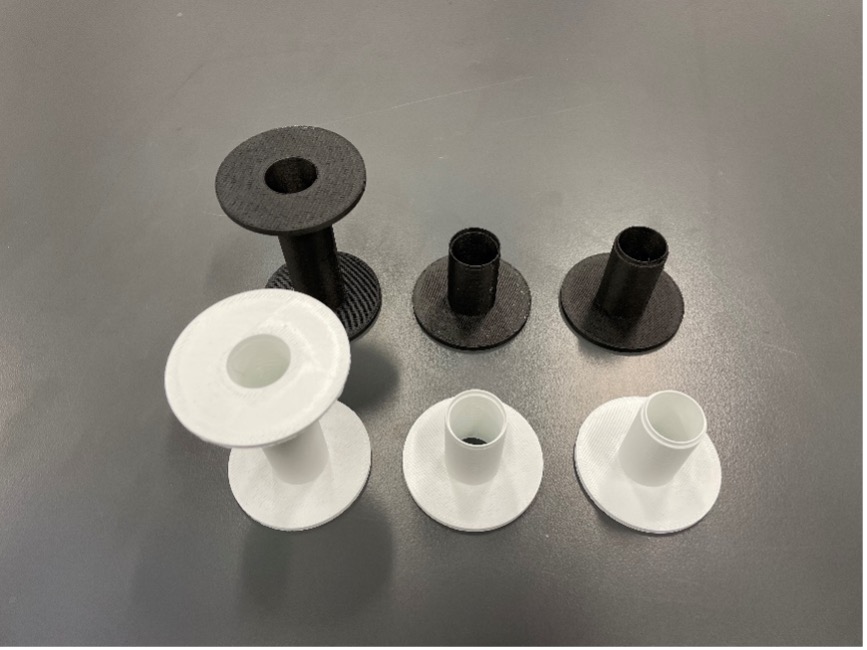