5 things to consider before 3D printing
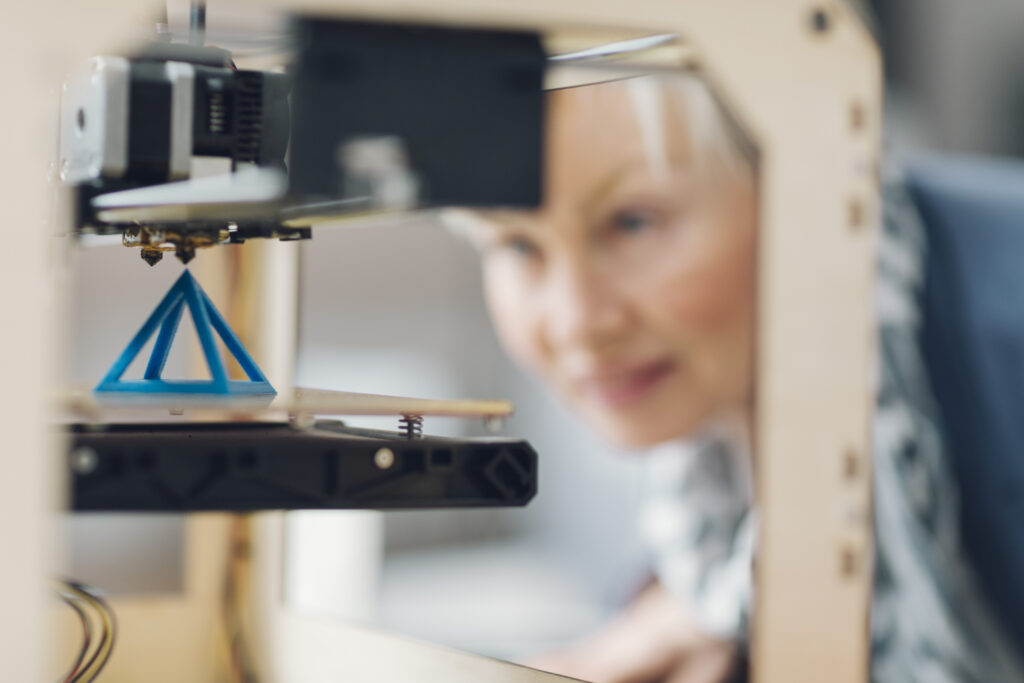
Andrew Conley, Additive Manufacturing Engineer, STFC
Often one of the hardest things when it comes to 3D printing (also known as Additive Manufacturing) is understanding the new approach to design that needs to be taken. Although 3D printing is increasingly being utilised as a quick and efficient method for product prototyping, it requires a whole new way of thinking, and designing, than traditional manufacturing processes (many businesses even develop two designs in parallel – one for 3D printing the initial prototypes, and one for mass manufacturing later down the line).
This is something that I’ve spent much of my career working with SME’s on – developing solutions to bring products to life using 3D printing technologies. Recently I’ve been working on projects ranging from assisted living to astronomical components.
No matter what the project, the same questions arise – what features can you create? How can you add additional strength? What is and isn’t possible?
It’s important to understand the differing design principles of 3D printing to maximise the benefits of the technology. I’ve collated this into my top five considerations for optimising your 3D printing.
1. Material matters
There’s a wide range of materials that it is possible to 3D print with, from Polylactic Acid (PLA) used in a range of desktop 3D printers, and providing an inexpensive and easy-to-use material for basic product prototyping, to metal, or carbon fibre filaments. This diversity of materials provides the ability to manipulate the properties of the design, conferring low-weight and high strength, flexibility, thermostability, transparency or chemical resistance, depending on what you’re trying to achieve. Think about the properties you need your product to have as one of your first considerations, this will help you identify a suitable material and 3D printing process.
2. Freestanding features
It’s vitally important to consider any structures in your design that are freestanding. Things like cylinders, clips, walls and unsupported overhangs need support when 3D printing, otherwise you may be looking at collapse on your hands (and a significant amount of wasted time and effort). This can be solved in most cases by integrating additional features such as a radius or a fillet, into the design from the outset. Alternatively, you can use a support structure generated in the 3D printing software, which will ensure the design is reinforced while printing, but make sure you consider how this will be removed after the print so that it is not part of the final product (there is a range of techniques to achieve this depending on the printing material used). Considering which features in your design are potentially problematic is essential to ensure you can effectively translate your ideas into the 3D printed world without disappointment.
3. Thick or thin
In traditional manufacturing processes, thin materials can be reinforced by adding a range of fixings to mitigate potential weaknesses.
However, as 3D printed designs are built in one continuous process with no added fixtures, thin walls and sections are vulnerable to collapse. When developing your 3D print design it’s important to think about how thick the walls of your features need to be. If they don’t reach the threshold, the robustness will almost certainly be compromised.
4. Holes & slots
If your design incorporates holes and slots, this is another big consideration. These features create weaknesses in the print and can collapse if not designed correctly (there’s a theme here!). Generally on our Mlab metal 3D printer if the hole or slot is small (approximately less than 5mm diameter) this can be printed with no support material. If it’s bigger, then there’s a range of options – incorporate support material in the design, change a circular hole to a more stable teardrop shape, or drill the hole in afterwards. It’s important to remember that while 3D printing is an effective solution for many things, sometimes traditional solutions can still be the most pragmatic.
5. Asking the expert
If you’re new to 3D printing, getting expert advice is often the differentiator between success and failure.
Get in touch with the team today to see how we can help you explore the 3D printing opportunities and supporting your business on your digital transformational projects.
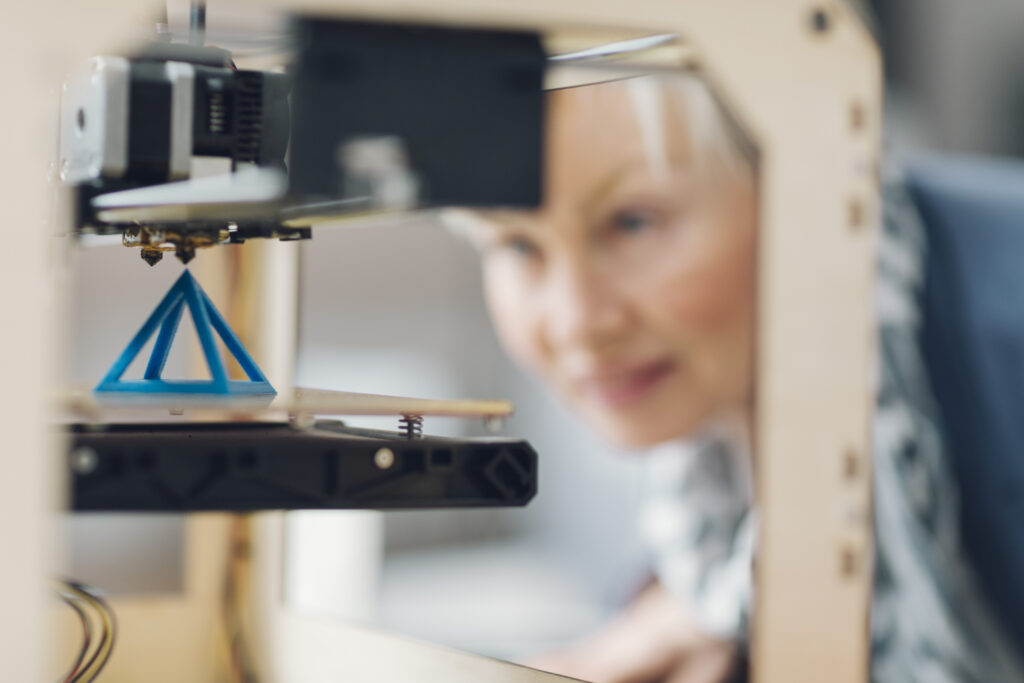
Explore more

Digital support for North West manufacturers set to deliver £100m GVA boost benefit for region
Evaluations of digital transformation initiatives, Cheshire & Warrington 4.0 (CW4.0) and LCR 4.0 Holistic, have…
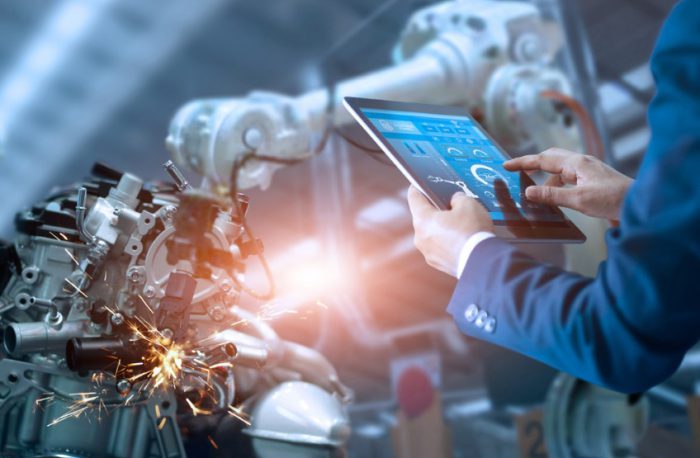
Digital innovation supporting jobs and business models in Covid-19 recovery
Increased adoption of new digital technology has underpinned businesses’ response to COVID-19, with four in…
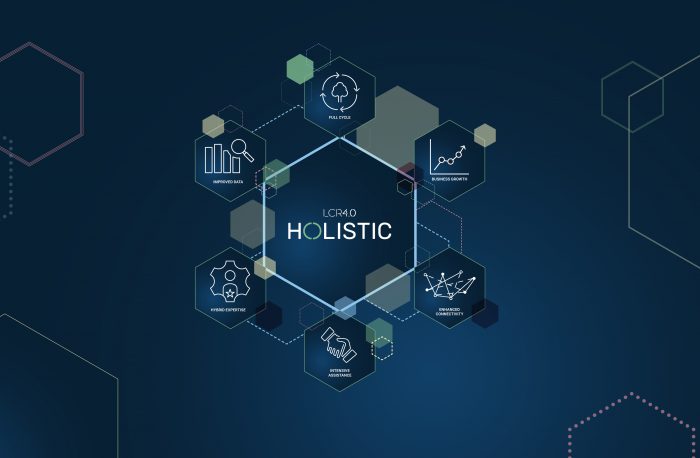
LCR4.0 Holistic supports over 50% more start-ups as a catalyst for Business Growth and Innovation
Since launching in the summer of 2020, LCR4.0 Holistic has been making great strides in…